3 The statistics in Table 1 were compiled for the 11B/11C MOS with percentages based on the population of Sergeants First Class (SFC) eligible for consideration for promotion to MSG The FY19 MSG Selection Board identified 222 out of 1,274 1 eligible CMF 11 SFCs for promotion to MSG resulting in a 174% selection rate This is 05%As it turns out, it makes a lot of difference but not the difference so many have assumed Read verse in The Message BibleMSG3 is now the preferred method used for developing the scheduled maintenance tasks and intervals which will be acceptable to Regulatory authorities, Operators, and Manufacturers This course is intended to support a deeper understanding of the Role of the Maintenance Process The role of MSG3 the obligations of the THC STCH and the Operator To promote an effective

Functional Reliability Centered Maintenance Rcm Module Pennant Ips
Msg 3 analysis example
Msg 3 analysis example-ATA MSG3 SHM WG Detailed Proposal Rev 1, dated 24 Aircraft Structural Analysis Procedure 242 Scheduled Structural Maintenance 9 Structural Monitoring Systems Structural Health Monitoring systems that are certified for their intended function may be used to ensure inherent airworthiness of the item being monitoredReliabilitycentered maintenance (RCM) is a concept of maintenance planning to ensure that systems continue to do what their user require in their present operating context Successful implementation of RCM will lead to increase in cost effectiveness, reliability, machine uptime, and a greater understanding of the level of risk that the organization is managing




Ulrica Pen In Aviation Aircraft Maintenance What Is Msg
The first step in MSG3 systems and powerplant analysis is to define the systems, subsystems, subsubsystems and parts that make up the aircraft For each component, the analysts review the available technical data, such as reliability and maintainability characteristics and description and operation documentation Both MSG2 and MSG3 analysis procedures/logic have been used to develop a majority of the routine scheduled maintenance and inspection programs of Transport Category Air Carriers (those that operate under 14 CFR 121 Title 14, Code of Federal Regulations, Part 121; MSG3, The Intelligent Maintenance Sign up for Aviation Pros eNewsletters SIGN UP Latest in Engines & Components Credit Lee Aerospace Windows Lee Aerospace Now Offers Learjet 55
Aeronovo specializes in MSG 3 Analysis Provide MSG3 topnotch training Experts for over years for high ranked aviation companies Learn More! MSG is short for monosodium glutamate It is a common food additive — with the enumber E621 — that is used to enhance flavor MSGUnderstand the MSG3 logic and then addresses the components of the MSG3 methodology Separate modules cover MSG3 specifics such as Structurally Significant Items (SSI), Zonal Maintenance and Lightning/High Intensity Radiated Field (L/HIRF) Analysis The course concludes with a look at MSG3 Management issues, and a summary of the course and
The course is designed principally to prepare the delegate for a role as a MSG3 Analyst It is aimed at aviation engineering organisations The course will also benefit anyone working within an MSG3 environment who needs a working understanding of the MSG3 process in order to function effectively and efficientlyAircraft maintenance MSG3 program creator ReliaSoft MPC is an MSG3 compliant maintenance program creator for the aircraft/aerospace industry The software has been designed to assist MSG3 working groups to perform Systems and Powerplant Analysis, Structural Analysis and/or ZonalL/HIRF Analysis in accordance with the MSG3 Operator/Manufacturer ScheduledPage 2 of 4 PTC Windchill® MSG3) PTCcom Data Sheet • Fully functional FMEA module enables endtoend failure mode and effects analysis or FMECA • Fully customizable reports communicate maintenance tasks and schedules to service teams or governing bodies Utilize MSG3 best practices • Improve aircraft safety, reliability, and availability




Hangars An Overview Sciencedirect Topics



Aviation Safety Management Systems A Comparative Analysis Between
The MSG3 systems analysis is a robust procedure based on scientific logic and engineering judgment and it has evolved over the last 30 years by constantly making incremental changes based on industry experiences These changes are brought about the participation of airlines, manufacturers and regulatory agencies through industry group meetings such as the AThe following reflects some of the major improvements and enhancements generated by MSG3 as compared to MSG2 1 Systems/Powerplant Treatment MSG3 adjusted the decision logic flow paths to provide a more rational procedure for task definition and a mor e straightforward and linear progression through the decision logic MSG3 logic took a "from the top down" or consequenceMSG31 Today, MSG3 is the only method used by commercial airplane manufacturers Policy states that the latest MSG analysis procedures must be used for the development of routine scheduled maintenance tasks for all new or derivative aircraft In MSG3, the structural inspection program is designed to provide



Aircraft Maintenance Management Training Expert Ammte Ruwi Fl Oman Business Data Index



Understanding Msg Pdf Reliability Engineering Federal Aviation Administration
The MSG3 module is integrated with RAM Commander Reliability and FMECA modules It divides the procedure into 7 steps including system definition, maintenance significant items selection, failure effect categorization, task selection and development and report generation The MSG3 module guides the user through the decisionmaking process maintenance programs under the current analysis process and policies for the MSG3 and Regulatory Maintenance Review Board Presented by industry experts experienced in the management and application of MSG3 and Maintenance Programs, their Development and Execution Contact us to participate in our upcoming courses in Atlanta, GA MSG3 is a Topdown process, which enables a step by step systematic analysis MSG3 delivers lower maintenance costs with typical savings ranging from 15% to 25% for the same aircraft type on




Pdf Glutamic Acid And Monosodium Glutamate Msg Market




Creating Initial Scheduled Maintenance Plans For Aircraft Msg 3 Reliasoft
Romans 3 So what difference does it make who's a Jew and who isn't, who has been trained in God's ways and who hasn't?Reliability & MSG3 Processes – Theory & Practical – 5 Days Reliability programs form an essential element of the continuing airworthiness process and in fact are mandatory when aircraft are managed using MSG methodology The purpose of a reliability program is to ensure that the aircraft maintenance program tasks are effective and their periodicity is adequate, in addition theSetting the configurable options for all MSG3 analyses in the current repository Systems and powerplant analysis Structural analysis Zonal and L/HIRF analysis How set and apply working group stamps How to define the status updates for a record How to import MPC hierarchies between projects For features that are specific to a particular



2



2
Evolution of Maintenance Programs MSG3 Systems & Power plant Procedure MSG3 Analysis MSG3 Logic Diagram Task Selection Interval Determination Review & SummaryMSG3 stands from Maintenance Steering Group The MSG3 is used as the base concept in developing the required tasks in conducting a scheduled maintenance The MSG3 task is categorized by three different categories The three categories in the MSG3 are 1 Airframe system tasks 2 Structural item tasks 3Aka, FAR 121) MSG3 is a significant procedural shift from MSG2
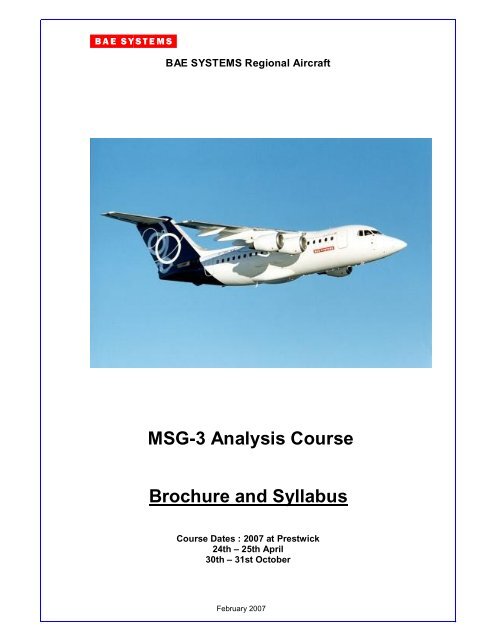



Msg 3 Analysis Course Brochure And Syllabus Regional Services




An Msg 3 Compliant Maintenance Program Msg 3 Compliant Maintenance Program Creator Msg 3 Systems And Powerplant Analysis Predefined Systems And Subsystems Based On Ata Ispec Pdf Document
Requirements revealed that, through the use of logical analysis and decision processes, it was possible to develop a program of applicable and effective maintenance tasks In 1968, the Maintenance Steering Group 1st Task Force (MSG1) developed maintenance requirements decision and analysis logicMaintenance Steering Group3 (MSG3) is a method for developing preventive maintenance programs in the aerospace industry The process is maintained by A (Airlines For America formerly known as ATA) MSG3 is a structured process for identifying Safety Significant Items (SSI), defining for each SSI the failure modes and effects (FMEA)MSG3 is intended to facilitate the development of initial scheduled maintenance programs The remaining maintenance, that is, nonscheduled or nonroutine maintenance, consists of maintenance actions to correct discrepancies noted during scheduled maintenance tasks, other nonscheduled maintenance, normal operation, or data analysis
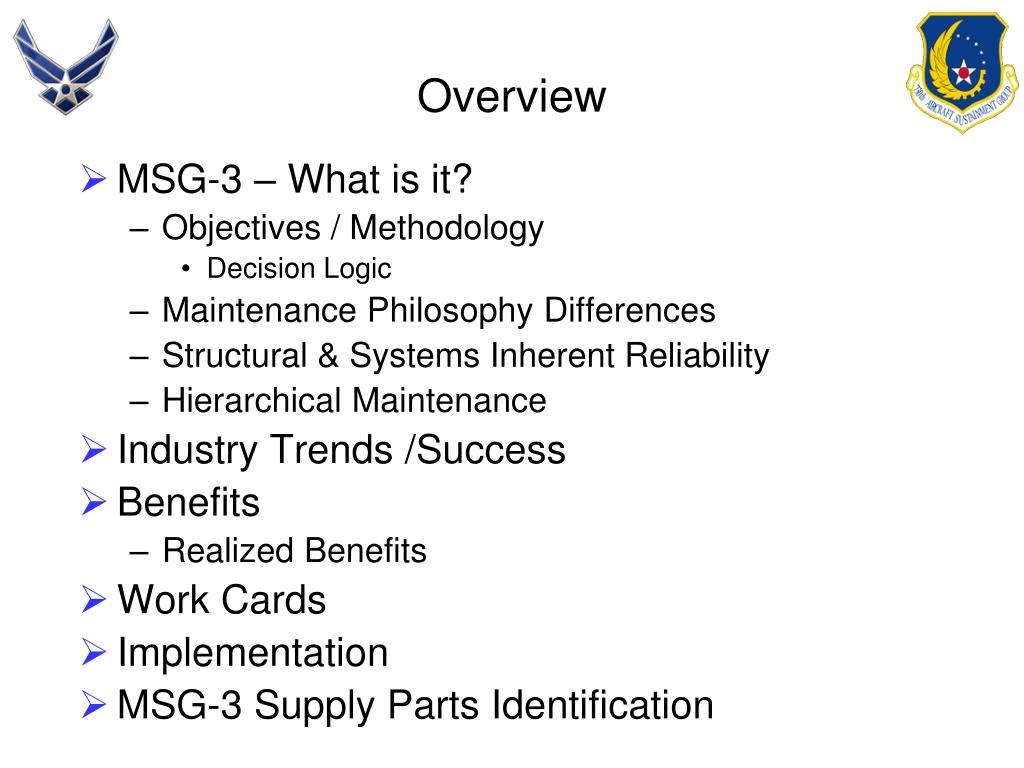



Ppt Maintenance Steering Group 3 Msg 3 Powerpoint Presentation Free Download Id 3244



Msg90
The MSG3 Rev 2 analysis established a common foundation for the 747 Classic and scheduled maintenance programs The commonality of the two programs aligns program execution as much as possible Because the format and organization of the maintenance programs are identical, administrative control of the programs is more straightforwardALD Ltd MSG3 Analysis FOR MSI Fuel Storage System Effectivity Xwing Fighter Spaceship Revision 3 Date 08/Process defined as MSG3 The process adopted a decision tree methodology with the primary purpose of a) separating safetyrelated items from economic, and b) defining adequate treatment of hidden functional failures Under MSG3 logic, activities are assessed at the system level rather than the component level – see Figure 3



2



Lifecycle Maintenance Home Facebook
ANALYSIS The first task to be performed when preparing an MSG3 aircraft structural analysis is the identification of candidate pieces of structure as structural significant items Manufacturers are best equipped to select structural significant items because of the necessary familiarity and rigor inherent in their structural designReliability Centered Maintenance and MSG3 " Reliability Centered Maintenance (RCM) is a standardized methodology to develop the maintenance plan of a newly designed product or system or an improvement of such In particular, MSG3 stablishes the standard methodology for the process in the aeronautic industry"MSG 3 (continued) Scheduled Maintenance Program – MSG3 has expanded the objectives of MSG2 The objectives of MSG3 still emphasize safety, reliability, and economy, but have gone beyond MSG2 by * Restoring equipment to specification once it has deteriorated * Collecting data to monitor equipment * Providing information that may be




Ulrica Pen In Aviation Aircraft Maintenance What Is Msg




Growth Rate Of Monosodium Glutamate Msg Treated And Control S Download Scientific Diagram
Three Analysis in MSG3 There are mainly three analysis in MSG3 System Analysis In system Analysis, the first thing needs to do is to find out the MSI, Maintenance Significant Items The experts will find it out through ATA chapter systems, then sub systems, subsub systems, into the end parts That's why we called it "from top to bottomWindchill MSG3 provides stepbystep guidance for identi fying and scheduling maintenance tasks for aircraft in accordance with the ATA standard MSG3 (Maintenance Steering Group Version 3) Contextsensitive questions derived from the standard are structured within logicenforced diagrams to guide the analyst through MSI (Maintenance Sig This paper thoroughly studied the methodology of CCMR analysis, clarified the relationship between CCMR analysis, specific risk analysis, and MSG3 analysis through discussion of a real certification program Provided a lessons learned case and reference to other aircraft type design and certification
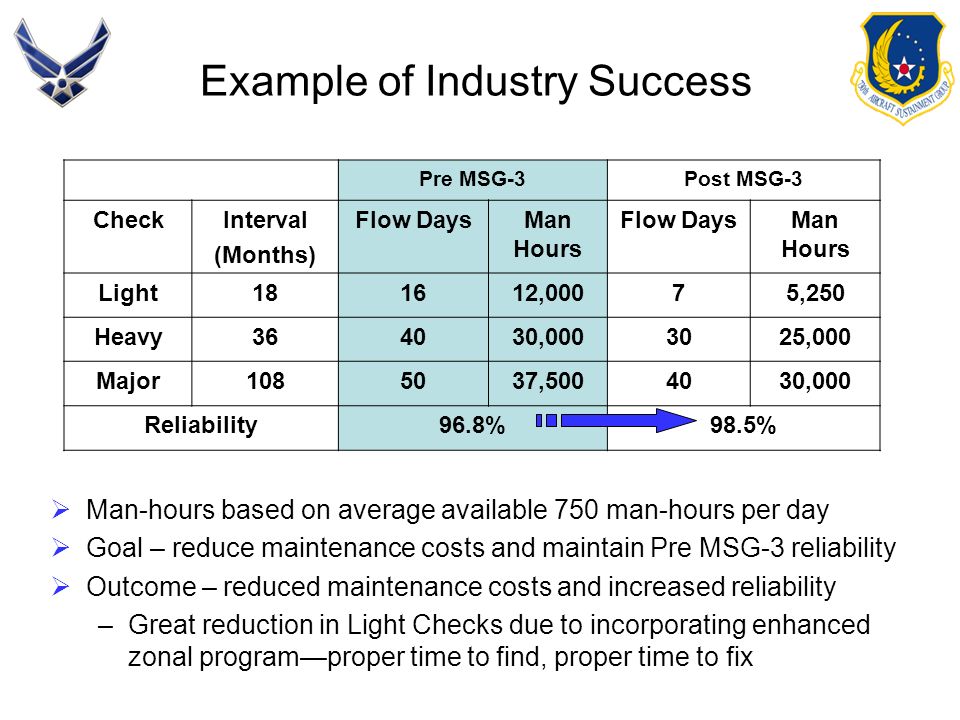



Maintenance Steering Group 3 Msg 3 Ppt Video Online Download




Msg 3 Maintenance Steering Group
RAMS (Reliability, Availability, Maintainability and Safety) Software Comprehensive software tool for Reliability and Maintainability Prediction, Reliability Analysis, Spares Optimization, FMEA/FMECA, Testability, Fault Tree Analysis, MSG3, Event Tree Analysis and Safety (SAE ARP4761, MILSTD8E)The 747 MSG3–based maintenance programs " The MSG3 analysis comprehensively and thoroughly identifies systems and power plant maintenance tasks and clearly separates safetyrelated tasks from those that are strictly economic The systems and power plant section in each MRBR identifies and addresses all safety itemsWith the introduction of MSG3 the maintenance focus changed from "bottomup" to "topdown" the process kept the concept of "hard time" & "on condition" but replaced "condition monitoring" with a "Zone Inspection Program" (ZIP) MSG3 is now the preferred method used for developing the scheduled maintenance tasks and intervals which will be acceptable to Regulatory




Creating Initial Scheduled Maintenance Plans For Aircraft Msg 3 Reliasoft
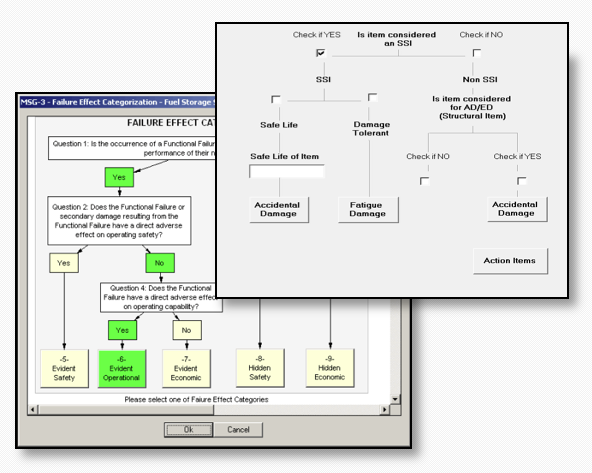



Reliability Centered Maintenance And Msg3 Dmd Solutions
RAM Commander MSG3 module is used by aircraft manufacturers or aircraft operators (airlines) to perform aircraft Scheduled Maintenance Development analysis according to Air Transport Association (ATA) Maintenance Steering Group 3 (MSG3) document According to ATA, the ATA MSG3 publication outlines a decisionlogic process for determining initial scheduledThis training includes a profound introduction into the MSG3 approach used to determine inspections and intervals (Scheduled Maintenance) for passenger and cargo aircraft In addition to this theoretical introduction training, we offer an individual onthejob training on the topics of MSG3 system, structural and / or zone analysisIn 1987, after applying MSG3 analysis procedures on a number of new aircraft and engines in the first half of the 1980s, the airline industry decided that the benefits of the experience gained during those years should be used to improve the document for future applications Thus, Revision 1 to MSG3 was developed
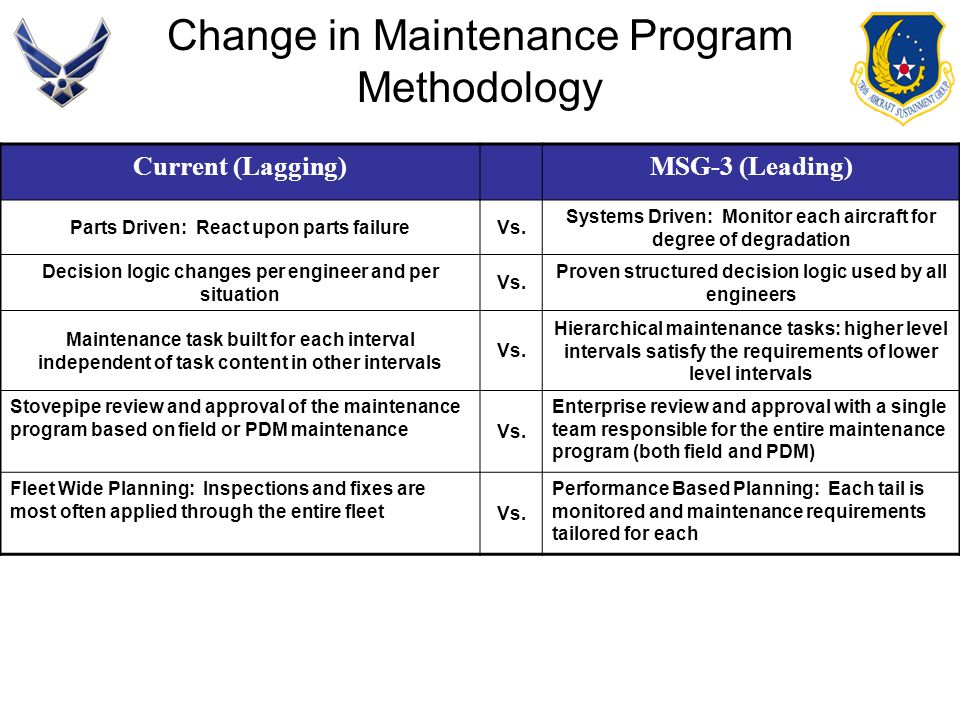



Maintenance Steering Group 3 Msg 3 Ppt Video Online Download
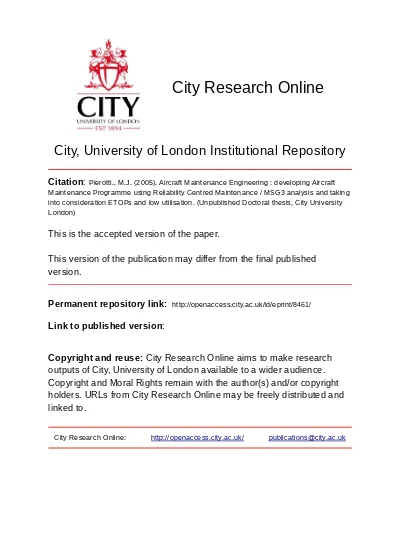



Aircraft Maintenance Engineering Developing Aircraft Maintenance Programme Using Reliability Centred Maintenance Msg3 Analysis And Taking Into Consideration Etops And Low Utilisation
MSG3 analysis should be applied to the complete certified aircraft, including the engines and propellers The MSG3 process and guidance is clear that the process applies to the entire aircraft, which would include the engine, APU, and/or propeller, as applicable Problem The MSG3 process requires analysis of the aircraft, which includes the MSG3 typically delivers a substantial cost reduction in hard time component removal and replacement MSG3 results in fewer maintenance tasks but not the importance of managing competencies Some MSG3 tasks are carried out for economic reasons, while others are carried out to deliver an improved safety levelMSG/3REPORT 21 MSG/3 Report on Agenda Item 2 REPORT ON AGENDA ITEM 2 FOLLOWUP ON THE OUTCOME OF MIDANPIRG/13 MEETING 21 The meeting was apprised of the outcome of the Thirteenth meeting of the Middle East Air Navigation Planning and Implementation Regional Group (MIDANPIRG/13) held in Abu Dhabi, UAE, 22 26 April 12



Sassofia Com
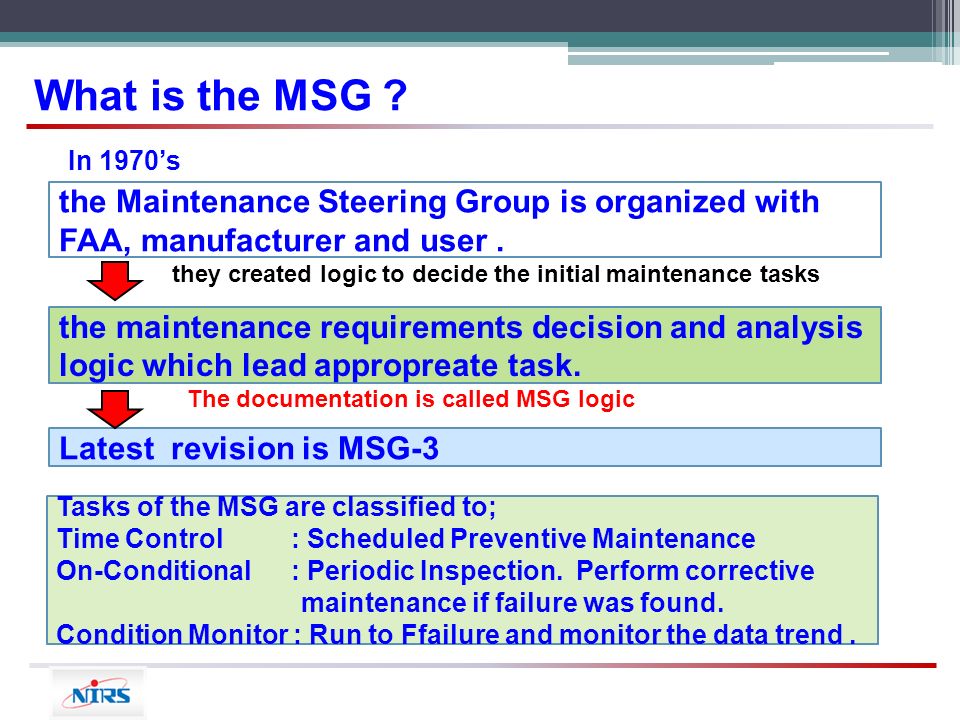



Intelligent Maintenance Program Ppt Video Online Download
Integration of MSG3 Into Airline Operation 8414 Implementation of the recommendations generated through MSG3 analysis is the major role of an airline operator in developing an initial maintenance program The accuracy and clarity of the MSG3 process provides a smooth transition for the airline to determine its manpower, parts, tooling



International Standard



2
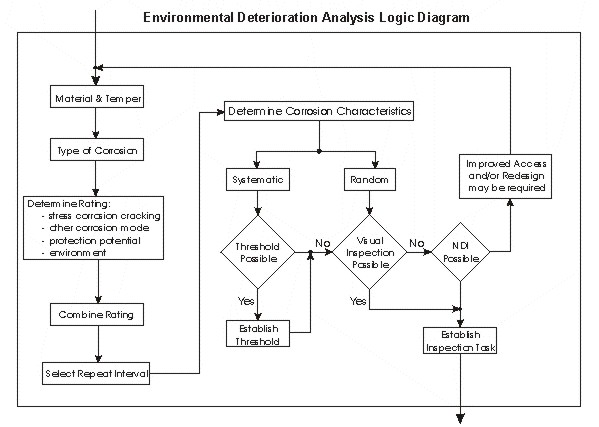



Maintenance Steering Group Environmental Deterioration Analysis Eda Flow Chart




Development Of Maintenance Programs Mcgraw Hill Education Access Engineering



2




Gsics Coordination Center Product Data




Metal Gear Solid 3 Analysis The 5 Phases Of Dealing With Hidden Trauma Keengamer
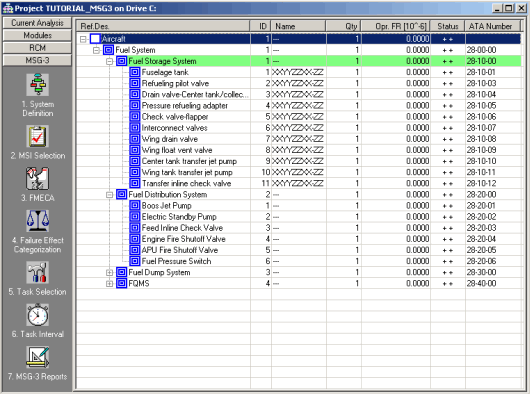



Msg 3
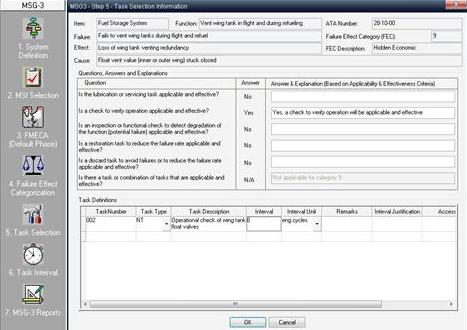



Msg 3 Module For Scheduled Maintenance



2




Pca Analysis Of The Samples Adding Msg Or Without Adding Msg By Download Scientific Diagram
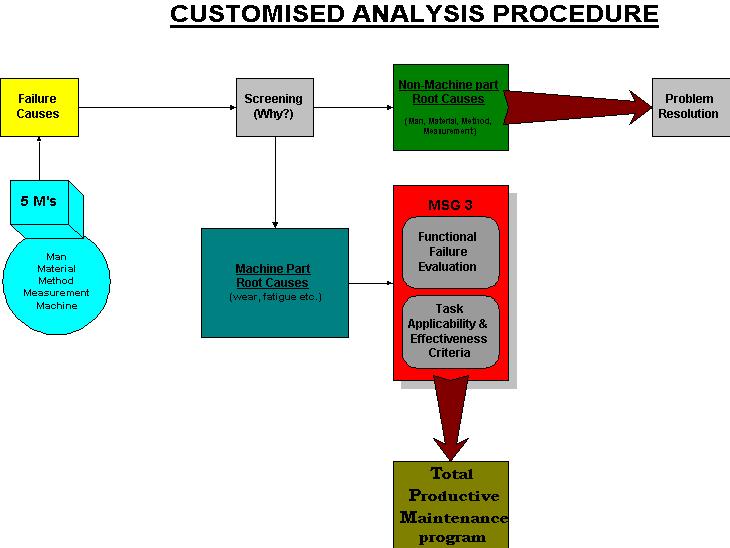



Uptime At Minimum Cost In The Process Industries



Msg3 Game




Msg 3 Logic Diagram
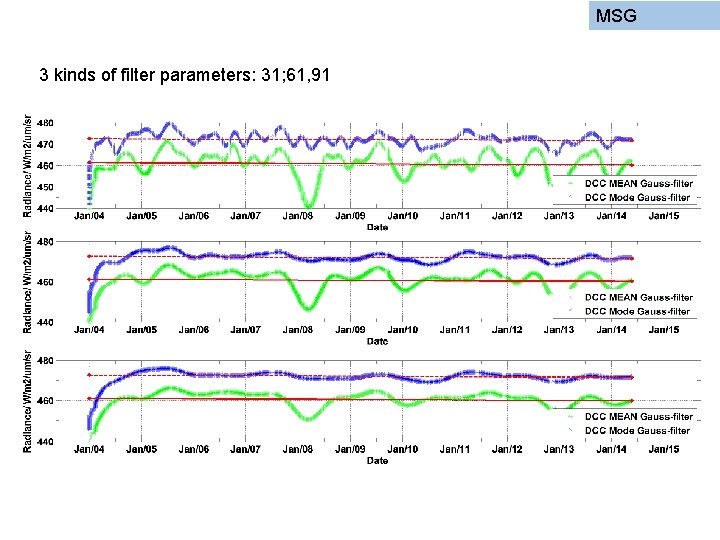



Dcc Analysis Lin Chen From Cma This Work
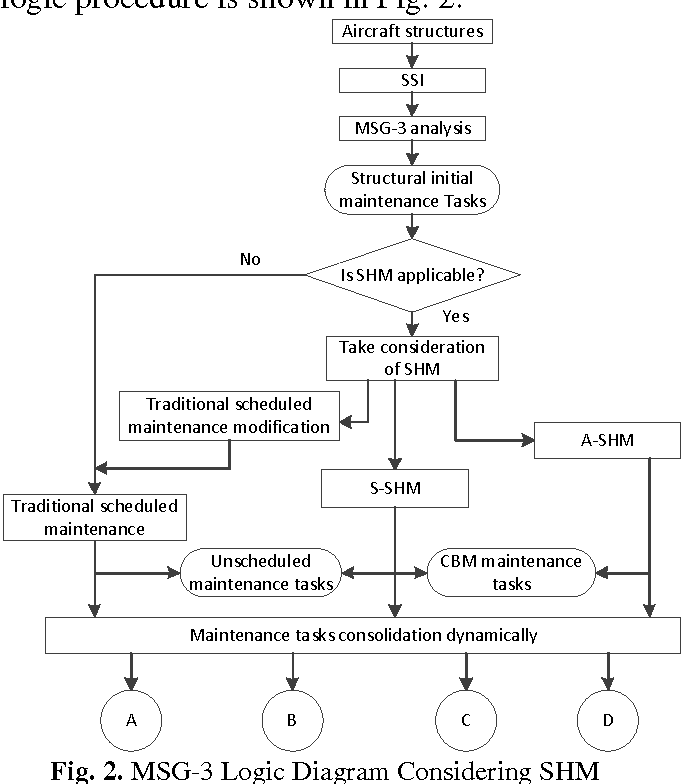



Pdf The Influence Of Shm Techniques On Scheduled Maintenance Of Aircraft Composite Structures Semantic Scholar




Maintenance Steering Group Fatigue Concepts



Rcm Sample




Msg 3 Maintenance Steering Group




Ulrica Pen In Aviation Aircraft Maintenance What Is Msg
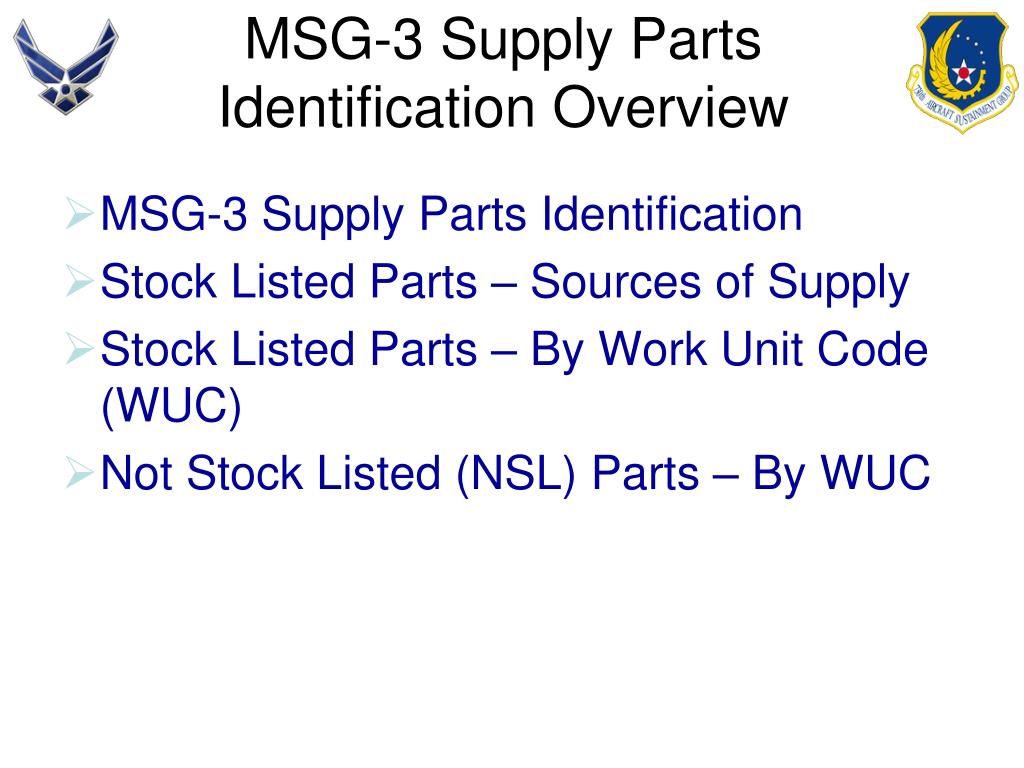



Ppt Maintenance Steering Group 3 Msg 3 Powerpoint Presentation Free Download Id 3244




Creating Initial Scheduled Maintenance Plans For Aircraft Msg 3 Reliasoft




Mpc Msg 3 Maintenance Program Creator Software Reliasoft
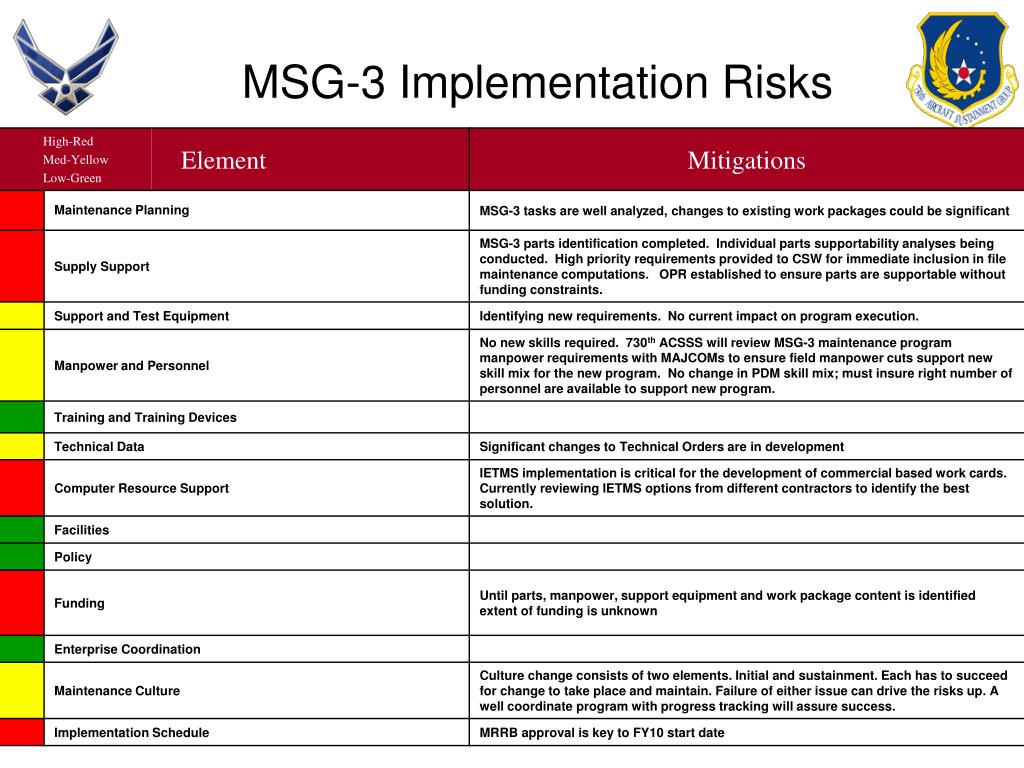



Ppt Maintenance Steering Group 3 Msg 3 Powerpoint Presentation Free Download Id 3244



2




Maintenance Steering Group 3 Msg 3 Based Maintenance Steering Group 3 Msg 3 Based Pdf Pdf4pro



2
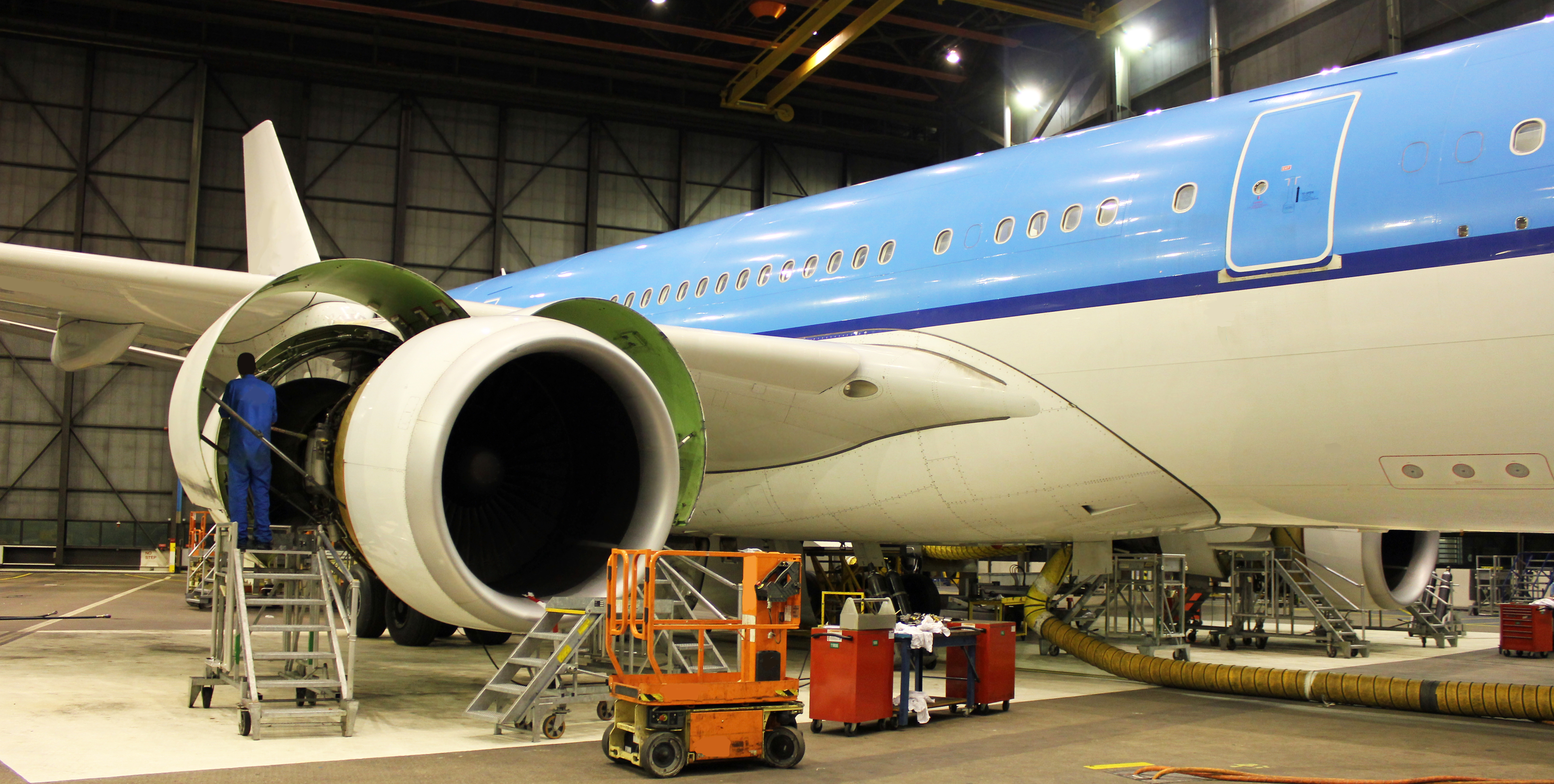



What S In An Msg 3 Inspection Sofema Aviation Servicessofema Aviation Services



Plos One Proteomic Analysis Of Kidney In Rats Chronically Exposed To Monosodium Glutamate



On Aircraft Scheduled Maintenance Program Development Emerald Insight
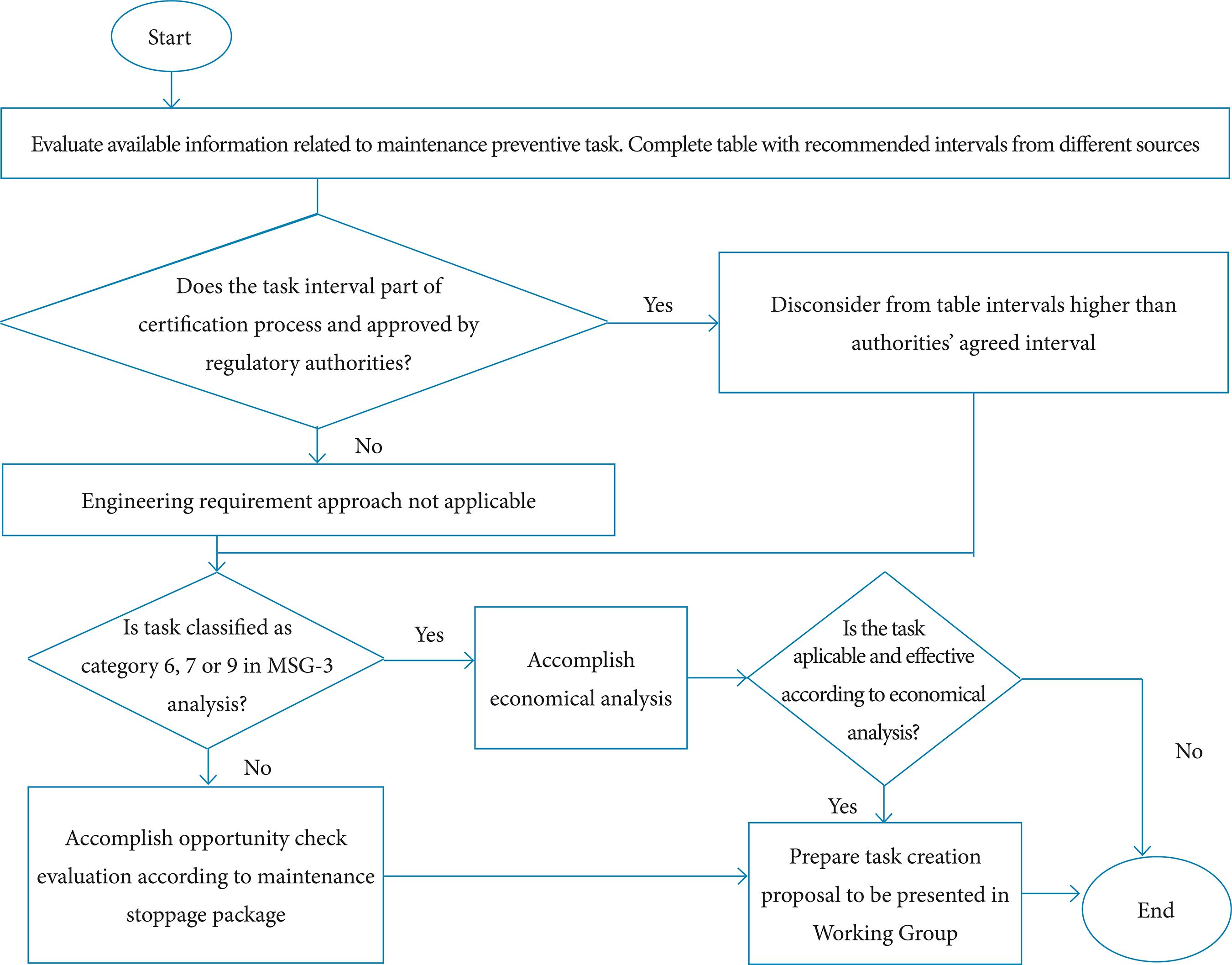



Scielo Brasil Aircraft Preventive Maintenance Data Evaluation Applied In Integrated Product Development Process Aircraft Preventive Maintenance Data Evaluation Applied In Integrated Product Development Process



Aula 14 Analise Msg 3 Zonal Pdf Electrical Wiring Aircraft



Maintenance Steering Group Environmental Deterioration Analysis Eda Flow Chart




Intelligent Maintenance Program Ppt Video Online Download
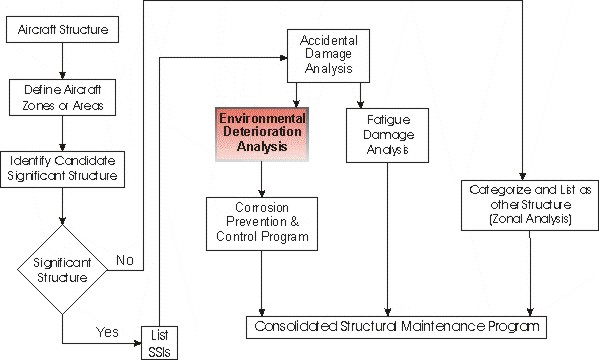



Maintenance Steering Group Structural Analysis Logic




Ulrica Pen In Aviation Aircraft Maintenance What Is Msg



2




Maintenance Steering Group Fatigue Concepts




An Msg 3 Compliant Maintenance Program Msg 3 Compliant Maintenance Program Creator Msg 3 Systems And Powerplant Analysis Predefined Systems And Subsystems Based On Ata Ispec Pdf Document




Functional Reliability Centered Maintenance Rcm Module Pennant Ips




Mpc Msg 3 Maintenance Program Creator Software Reliasoft




What Is The Difference Between Msg1 Msg2 And Msg3 Aviation Nuggets
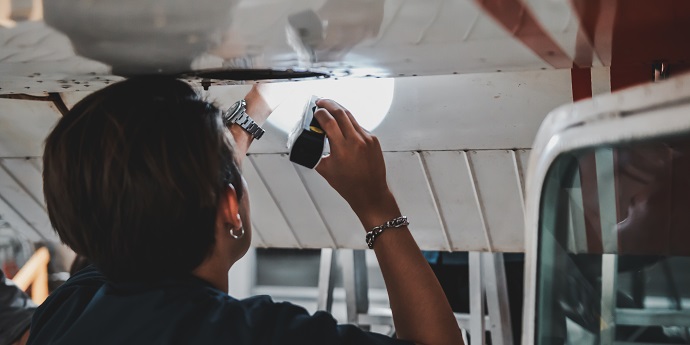



Msg 3 Aircraft Inspection Considerations Sofema Aviation Servicessofema Aviation Services




Maintenance Steering Group Fatigue Concepts




Metal Gear Solid 3 Snake Eater Wikipedia




Maintainability Analysis Robin Rams Software Suite



Aula 14 Analise Msg 3 Zonal Pdf Electrical Wiring Aircraft




Ulrica Pen In Aviation Aircraft Maintenance What Is Msg




International Specification For Developing Scheduled Maintenance Programs Pdf Free Download




Development Of Maintenance Programs Mcgraw Hill Education Access Engineering
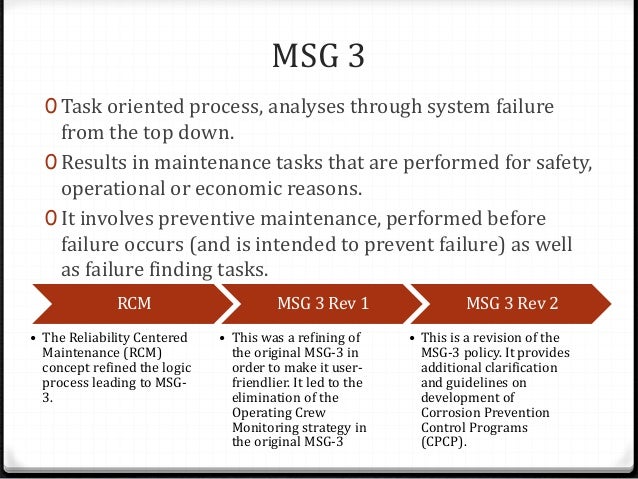



Aircraft Maintenance Program




Reliability Centered Maintenance And Msg3 Dmd Solutions




Maintainability Analysis Robin Rams Software Suite
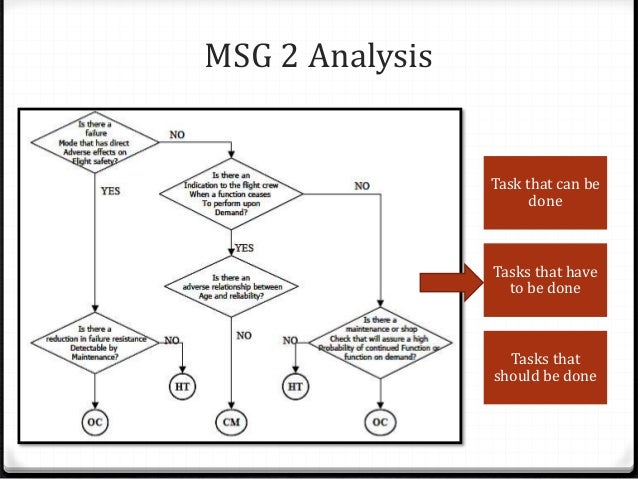



Aircraft Maintenance Program




Maintenance Steering Group Fatigue Concepts




Msg 3 Maintenance Steering Group




Analysis Of Aircraft Maintenance Processes And Cost Sciencedirect
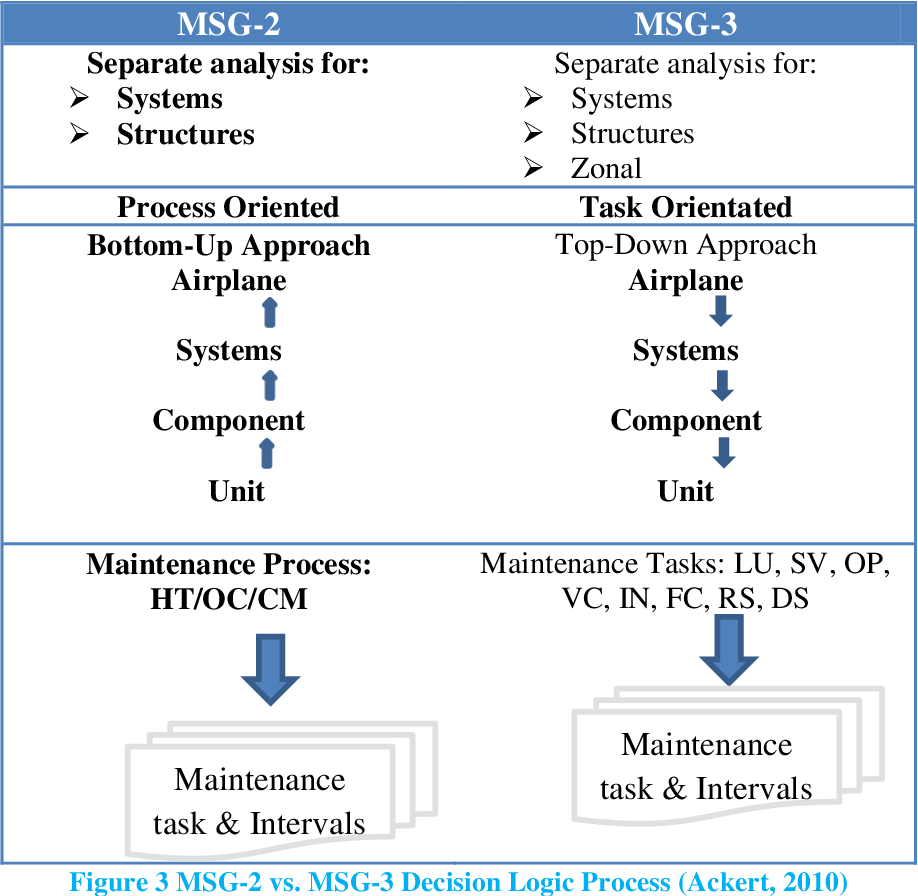



Aircraft Maintenance Cost Modelling Considering The Influence Of Design Parameters Semantic Scholar
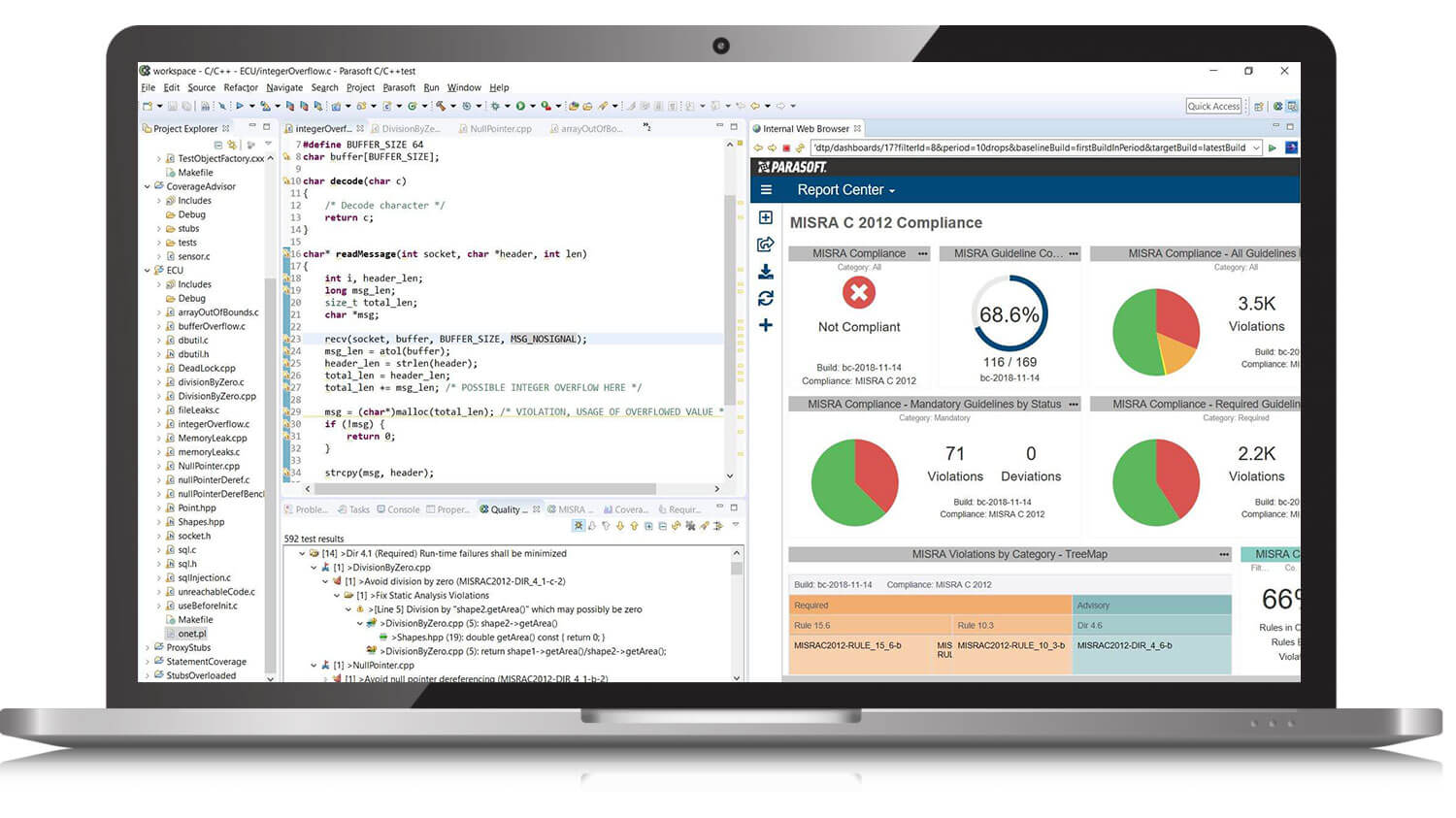



Static Code Analysis Tools For High Quality Compliant Code
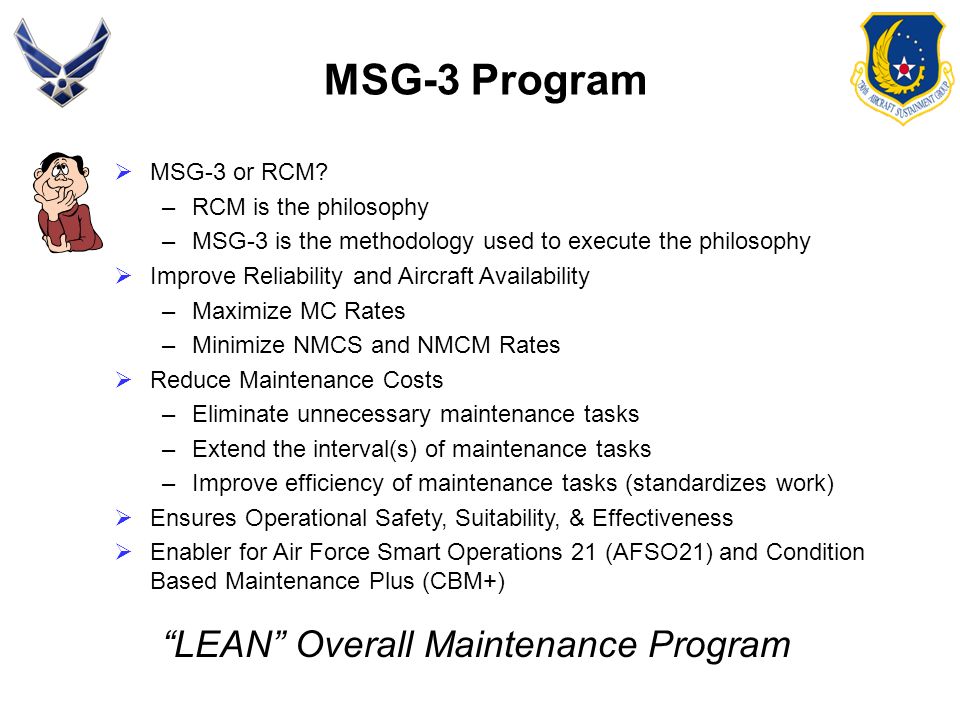



Maintenance Steering Group 3 Msg 3 Ppt Video Online Download



2




Creating Initial Scheduled Maintenance Plans For Aircraft Msg 3 Reliasoft



2



Sharetechnote



2




Maintenance Steering Group Fatigue Concepts




Ppt Maintenance Steering Group 3 Msg 3 Powerpoint Presentation Free Download Id 3244




Ulrica Pen In Aviation Aircraft Maintenance What Is Msg




Reliability Centered Maintenance And Msg3 Dmd Solutions



2
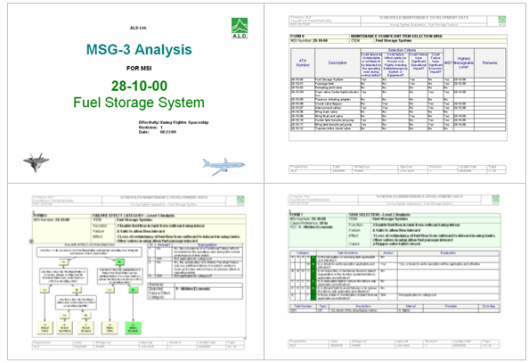



Msg 3
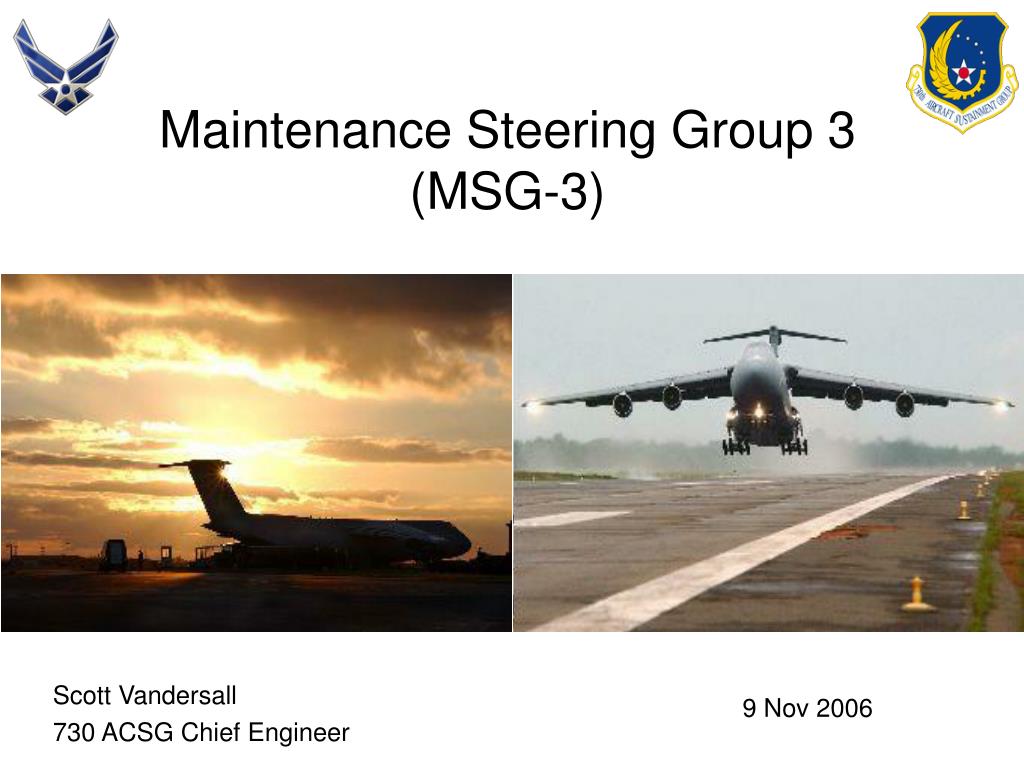



Ppt Maintenance Steering Group 3 Msg 3 Powerpoint Presentation Free Download Id 3244
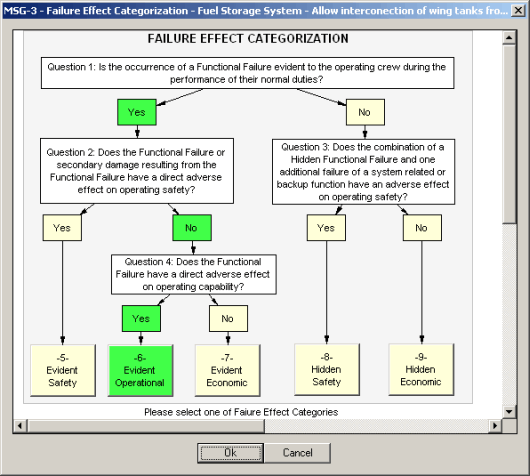



Msg 3
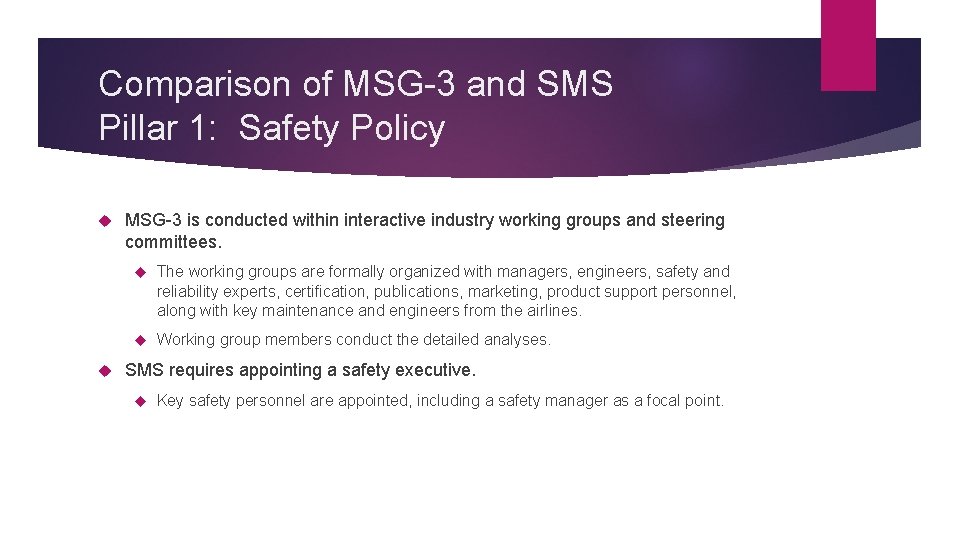



Aviation Safety Management Systems A Comparative Analysis Between




Benefits Of Optimizing Maintenance Intervals Pdf Free Download




Visor Redalyc Aircraft Preventive Maintenance Data Evaluation Applied In Integrated Product Development Process



2
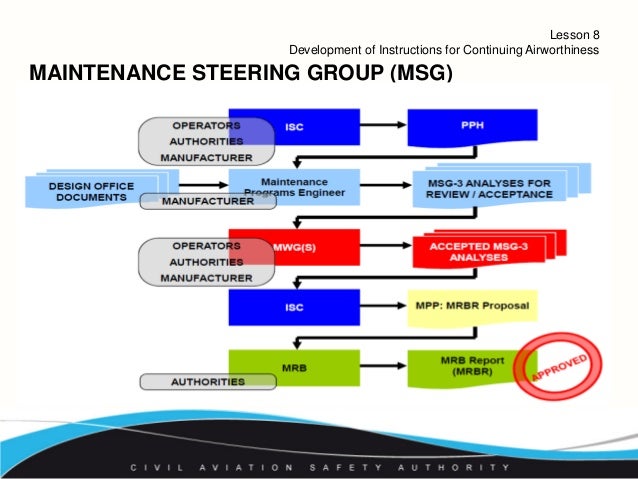



Cmr
0 件のコメント:
コメントを投稿